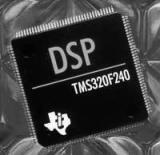
The TMS 320F24x is a series of specialized Digital Signal Processors (DSP) for
the motor control and embedded process automation realm. We used this processor
in two three phase control projects. One involving a motor and inverter, the other
involving an inverter only.
The device features a standard TI core with a harvard architecture with an independent data
flow for optimal parallelism
in signal processing and control algorithms. Many control applications include
digital filtering. Some control algorithms are mathematically equivalent to a digital filter. The DSP core is optimized for these tasks in many ways. One example is the
"MACD" instruction, that performs a "multiply", an "add" and a "data move" within one
cycle (50 nS) if repeated in a loop.
The specialty of the TMS 320F24x lies in the on chip peripherals. The two
independent 10 Bit S/H converters allow conversion times in the range of a few
microseconds and form a complete acquisition subsystem. The "event manager" includes
multiple timers and a sophisticated high resolution PWM stage with multiple
independent outputs.
The Space Vector Modulation is ideal for motor and inverter control. The algorithm
is already realized in hardware, the control software needs to compute the
vectors only, pulse generation is automatically performed by the event manager.
The processor's JTAG interface allows real time emulation of the hardware design
without the need for an expensive hardware emulator. The flash memory can be programmed on
board, allowing easy software updates anytime during product life.
A
comprehensive set of development tools
allows quick program development in either C or assembler. Libraries and
complete motor control software is available through TI's extensive third
party network.
For further information regarding Ti products and the motor control DSP's click
here. 